A differential pressure (DP) flowmeter consists of a differential pressure transmitter integrated with a primary element. In the past, pressure transmitter companies sold DP transmitters and users ordered their primary elements separately. Now companies are selling their DP transmitters already integrated with a primary element, such as an Annubar or an orifice plate. When a DP pressure transmitter is integrated with a primary element and has the capability of calculating flowrate based on difference in pressure, it is a DP
flowmeter.
DP flowmeters rely on a constriction placed in the flow line that creates reduced pressure in the line after the constriction. They also require a means to detect the difference in upstream vs. downstream pressure in the flow line. While this can be done with a manometer, today’s DP flowmeters use differential pressure transmitters that sense the difference in pressure, and then use this value to compute flowrate.
Theory of differential pressure measurement
The theory behind DP flowmeters is that energy is conserved when flow passes across or through a constriction in the pipe. A more exact statement of this theory is known as Bernoulli’s principle, which states that the sum of the fluid’s static energy, kinetic energy, and potential energy is conserved across a constriction in the pipe. One form of Bernoulli’s principle for incompressible fluids is as follows:
V2/2g + z + P/ρg = constant
V is the velocity of the fluid, g is the acceleration constant, P is pressure, ρ is density, and z is the elevation head of the fluid.
The equation of continuity formulates a relation between fluid flowrate and velocity for fluids that are incompressible. It can be formulated as follows:
Q = A1 x v1 = A2 x v2
Q is volumetric flowrate. The product of A1, the amount of an incompressible fluid that crosses the area at point 1 over some set amount of time, times v1, the velocity at point 1, equals the product of A2, the amount of fluid that crosses the area at point 2 over the same set amount of time, times v2, the velocity at point 2.
Click to learn
more about other technologies in:
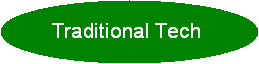
More info on DP Flow:
www.flowdp.com
www.FlowElement.com
DP flow in ancient Rome?
The history of DP flow measurement goes back to at least the 17th century, though the measurement of flow using nozzles actually goes back to Roman times. At the beginning of the 17th century, Torricelli and Castelli arrived at the concepts that underlie differential pressure measurement today -- that flowrate equals velocity times pipe area, and that the flow through an orifice varies with the square root of the head. In 1738, Bernoulli developed his famous equation for flowrate calculation.
The development of primary elements for use in measuring DP flow also began about this time. Pitot presented a paper on the use of the “Pitot tube” in 1732. Venturi published his work on the Venturi principle for measuring flow in 1797. However, Venturi’s work was not developed for commercial application until 1887 when Clemens Herschel used Venturi’s work to develop the first commercial flowmeter based on it. In 1898, Herschel published his paper, “The Venturi Water Meter.” Max Gehre received one of the first patents on orifice flowmeters in 1896.
The first commercial orifice plate flowmeter appeared in 1909, and was used to measure steam flow. Shortly thereafter, the oil and gas industries began using orifice plate flowmeters due to ease of standardization and low maintenance.
Researching the DP market
Suppliers
and manufacturers of DP transmitters
Advances in pressure transmitters
Over the past several years, pressure transmitter suppliers have released a number of new products with advanced features. These features promise higher accuracy, greater reliability, enhanced self-diagnostics, and more advanced communication protocols.
The promise of greater reliability is perhaps the strongest driving force behind the pressure transmitter market. While some products may have a higher initial purchase price, end-users cite a number of reasons for shifting to higher performing products. These include the need to conform to regulatory requirements, the need for reliability, a desire to standardize pressure products, and the need to do custody transfer.
Advances in primary elements
Primary elements suppliers have
also made a number of technological improvements:
-
Emerson Rosemount introduced a conditioning orifice plate that reduces the upstream requirements for a DP flow measurement.
-
Veris introduced the Accelabar, which combines elements of a flow nozzle with elements of an averaging Pitot tube.
-
Emerson Daniel upgraded its Senior Orifice Fitting with the release of the new Senior Model 2000 Orifice Fitting designed for longer life and lower cost of ownership. Its check valves and O-rings are designed to prevent the escape of any potentially harmful content through the valve. Both Emerson’s Senior and Junior Orifice Fittings are widely used in custody transfer gas flow measurement.
More
on primary elements:
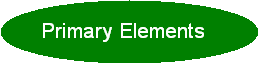
|